STEREQUIP
SOLUTION
More Health Service Organisations are realising the true benefit of external reprocessing of reusable medical devices.
YOUR TRUSTED PARTNER
We know Health Services only partner with trusted companies that deliver excellence.
That’s why when you choose a Sterequip solution your Health Service can benefit in three ways.
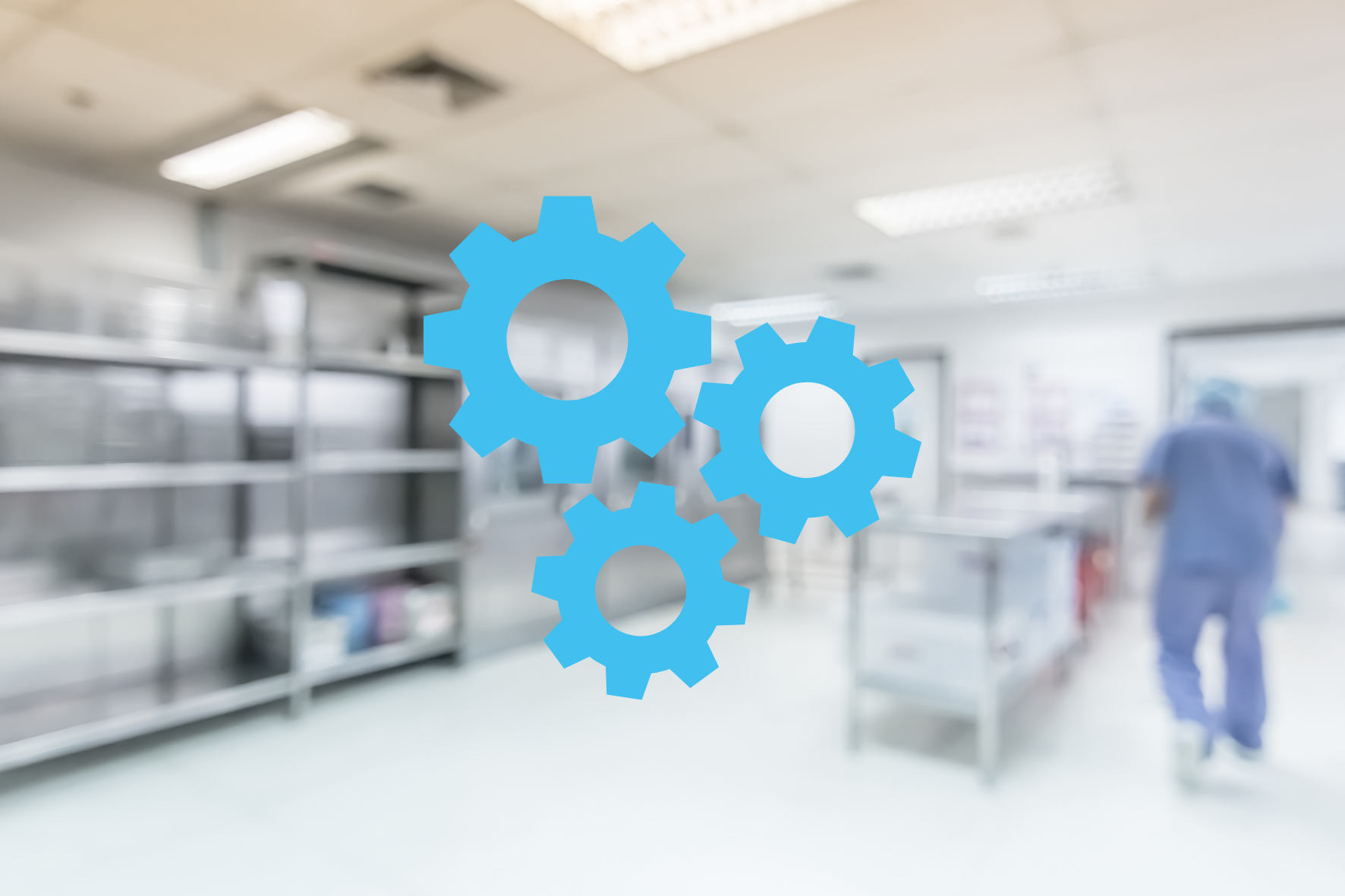
Operational Excellence
Sterequip provide operationally excellent systems and processes to minimise risk. Importantly, Sterequip are able to provide cost effective compliant reprocessing solutions for your health service.
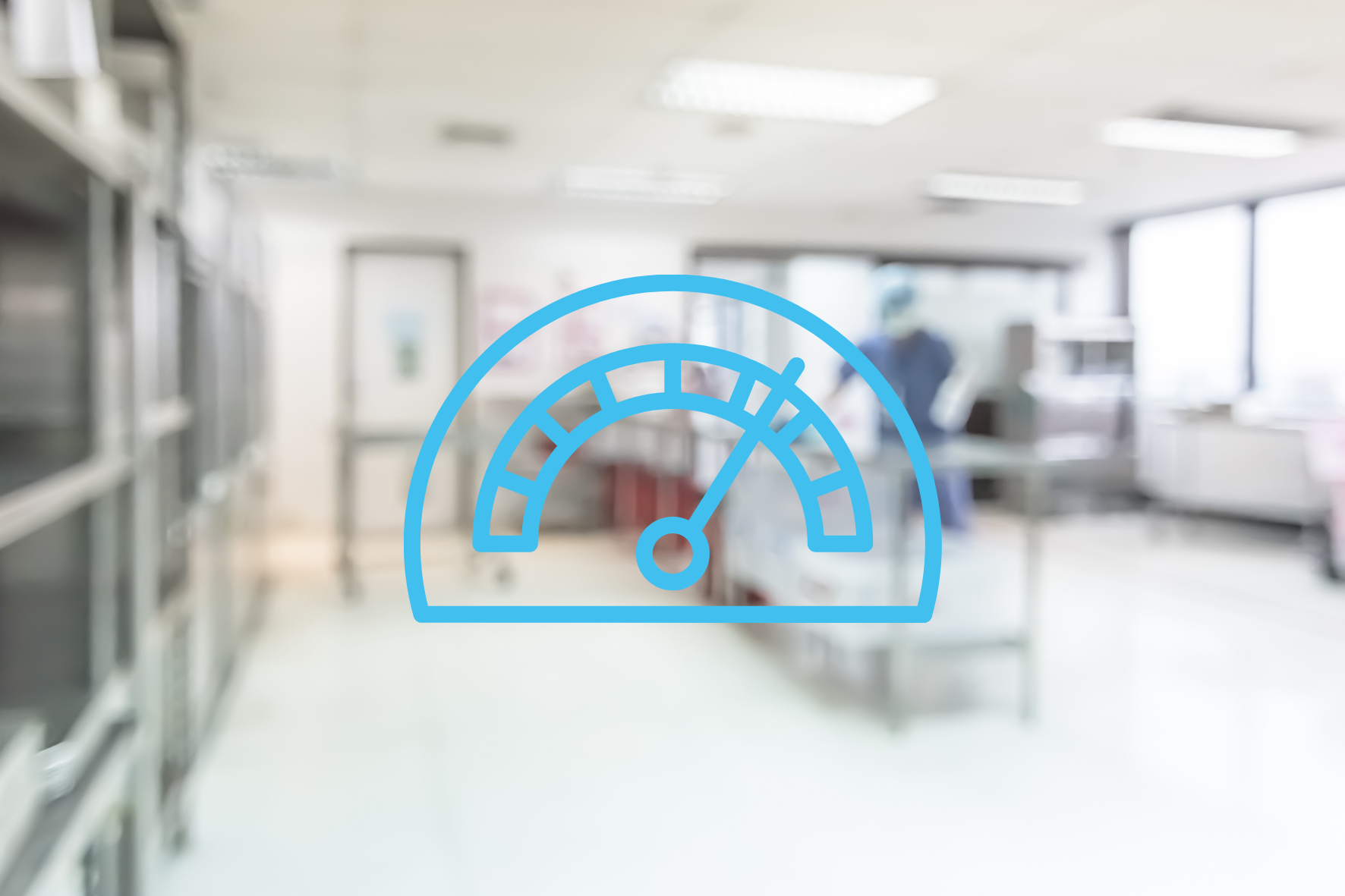
Greater Capacity
When you choose an external reprocessing solution you can secure capacity for your current and future growth. An additional benefit is repurposing existing CSSD space into higher value activities.
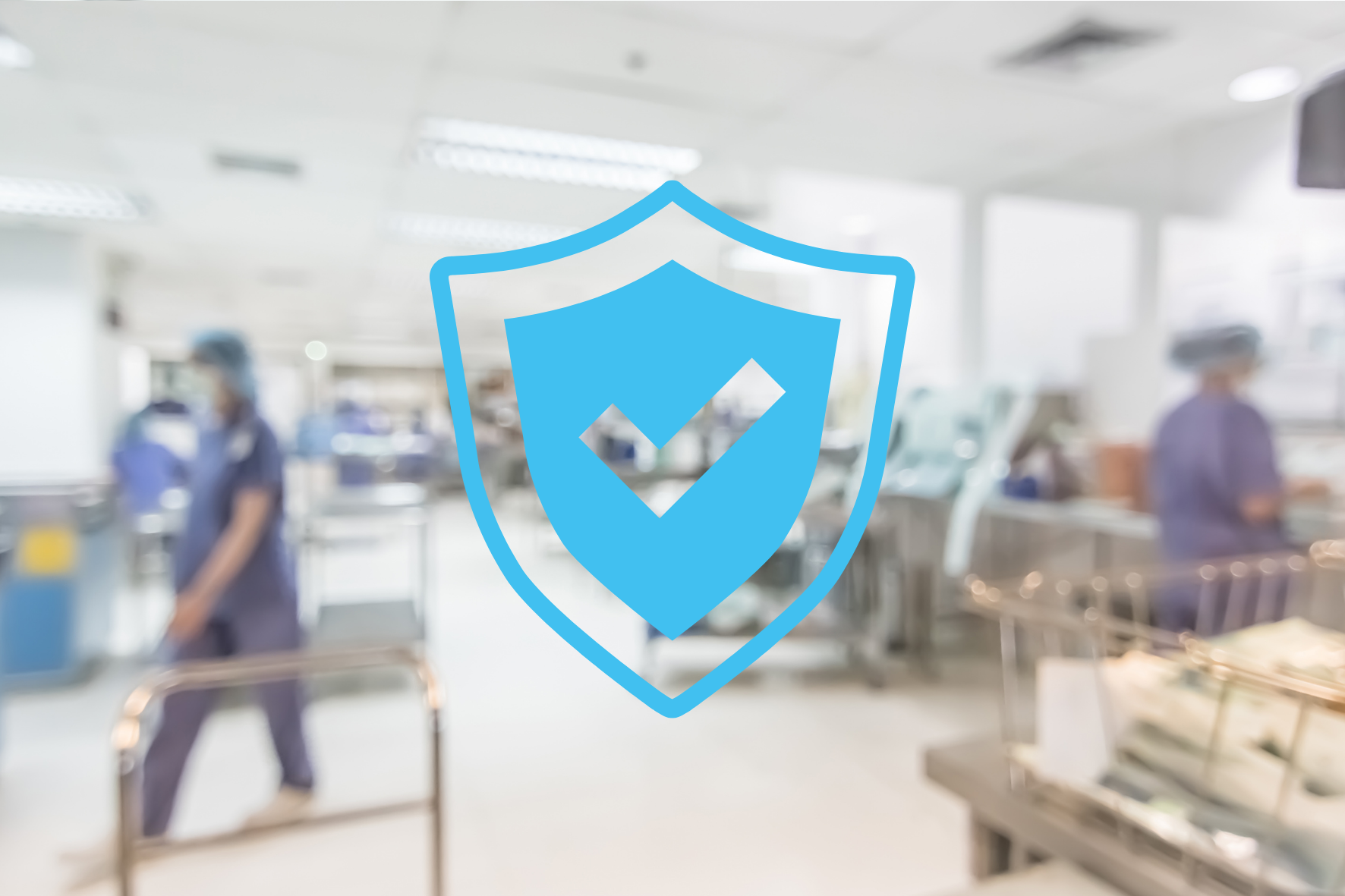
Compliance Ease
For many staying compliant to new standards can be difficult and arduous. Sterequip provides a variety of solutions that helps health services meet the compliance requirements of today and for the future.
It’s time to discover how Sterequip can benefit your Health Service.
Contact us today on 1300 783 737
THE RIGHT CHOICE
Sterequip provides your Health Service Organisation with reprocessing to meet
AS 5369:2023, the Australian Standard for Reprocessing of reusable medical devices and other devices in health and non-health related facilities.
Quality Reprocessing
- Daily collection of your reusable medical devices.
- Best practice reprocessing of your devices at our state-of-the-art facilities.
- Health Service Organisation to provide all instruments and replacements.
- Timely return of your sterilised reusable medical devices.
- Inspection of reusable medical devices. All devices identified as requiring maintenance or repair are thermally disinfected and returned with documentation.
- Traceability of marked trays via Sterequip portal.
- High quality service includes Washer soil testing in every load, Steriliser (Type 6 PCD) load checks with every cycle, protein tests, and Type 6 in-pack indicators in every container or pouch.
YOUR NEW WORKFLOW
The Sterequip process seamlessly integrates into your existing workflows with minimal disruption.
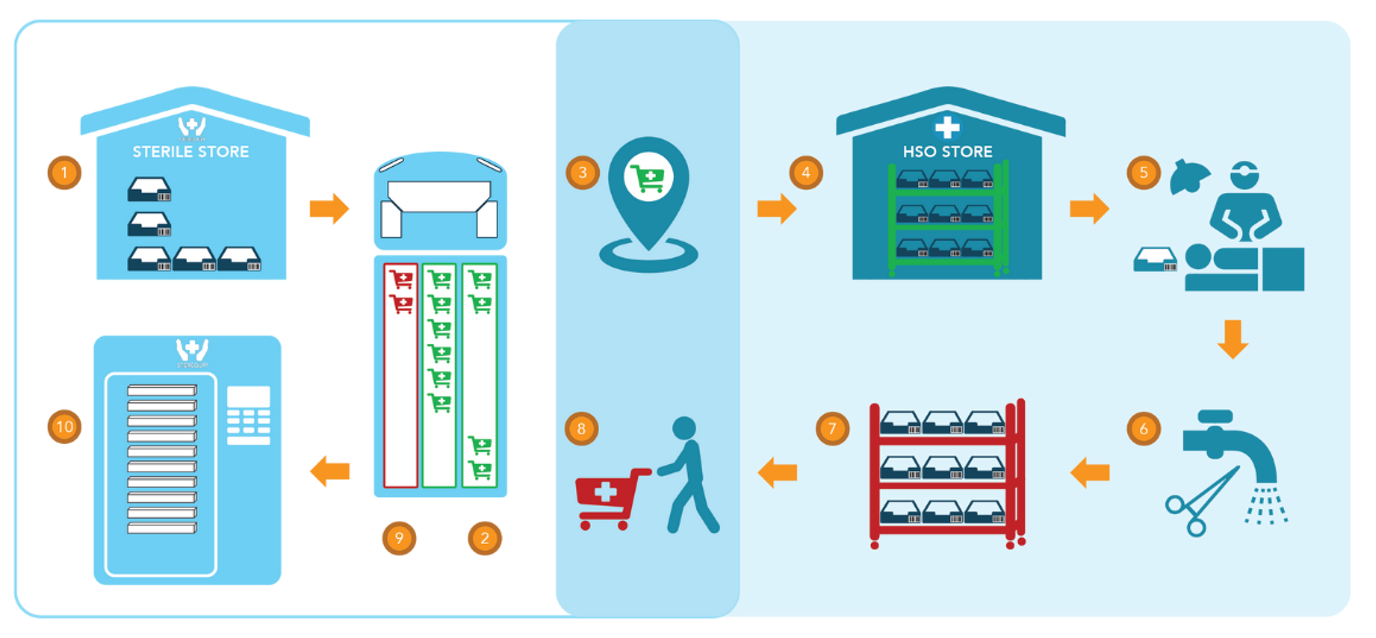
1. Sterile devices are stored at the Sterequip Sterile Store, ready for dispatch.
2. Once dispatched, they are transported to your health service in clean trolleys. These trolleys are transported by a UV disinfected, temperature-controlled transport vehicle’s clean compartment.
3. Trolleys are handed over to your health service at a designated receival point.
4. Devices and spares are stored ready for use at your health service sterile store.
5. Devices are then used.
6. Sharps and Gross Soil is removed by the health service.
7. Trays are placed back in the transport trolley ready for pick up.
8. Trolleys are then picked up and placed into a separate compartment of the transport vehicle.
9. Trolleys are then returned to the Sterequip Reprocessing Super Centre.
10. Devices are reprocessed in accordance with AS 5369 and stored at the Sterequip Sterile Store.
Income Generating Opportunities & Better Utilisation of Capital
It’s not just about meeting the critical and urgent needs of your hospital that makes Sterequip a compelling solution. It’s about providing you the opportunity to transform cost centres into income generating opportunities.
With Sterequip your health service can utilise the valuable CSSD space for higher use activities such as theatres or treatment rooms.
Better utilisation of capital into income generating activities allows your health service to grow providing a competitive advantage for your facilities.
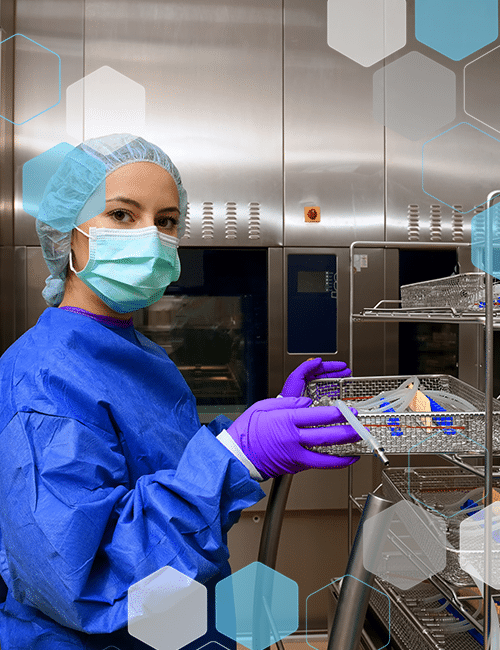
Secure Future Capacity
The cost of major infrastructure renovations, new equipment, water and air quality, sterile storage and electronic traceability systems to meet the standard now and in the future will be significant.
Costs escalate especially where space is limited. The space required to house new utilities, larger equipment and allowance for segregation of the workflow, will impact many health services that simply don’t have space in critical areas.
Sterequip can provide either a complete external CSSD solution or manage certain lines or loan equipment to allow your facility to manage growth more effectively.
This means no interruption to your services as you grow or as the standard changes.
Manage Multi-Site Requirements
Health service groups with several sites means the requirements can differ significantly. From preferred times for pick-up and delivery, to volume, instrument type and specialist physician’s personal instruments.
Sterequip provides tracking and tracing systems to give you 24 hours access to know where your instruments are and manage them as you need.
Our transport solution includes a fleet of temperature controlled and humidity monitored vehicles, designed to segregate used and clean transport trolleys.
With Sterequip we partner with each of your facilities to understand their individual requirements.
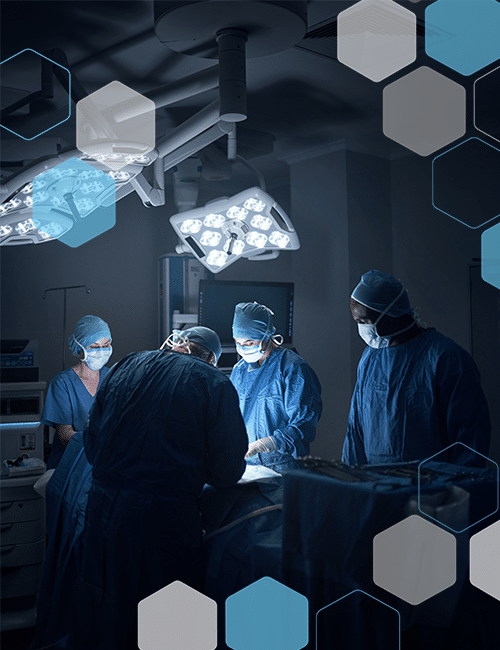
Improving Patient Outcomes
Sterequip has a team committed to provide the highest quality service to your organisation. Our team of skilled personnel are experts at reprocessing and across instrument manufacturers specific requirements to ensure any device is reprocessed correctly every time.
The design of our Reprocessing Super Centres has separate workflows that allow Sterequip to quarantine a workflow if necessary.
Your health service has complete visibility of all your instruments through our tracking and traceability systems, so you can manage all the data relating to instruments used on your patients.
PROUD
SPONSORS OF
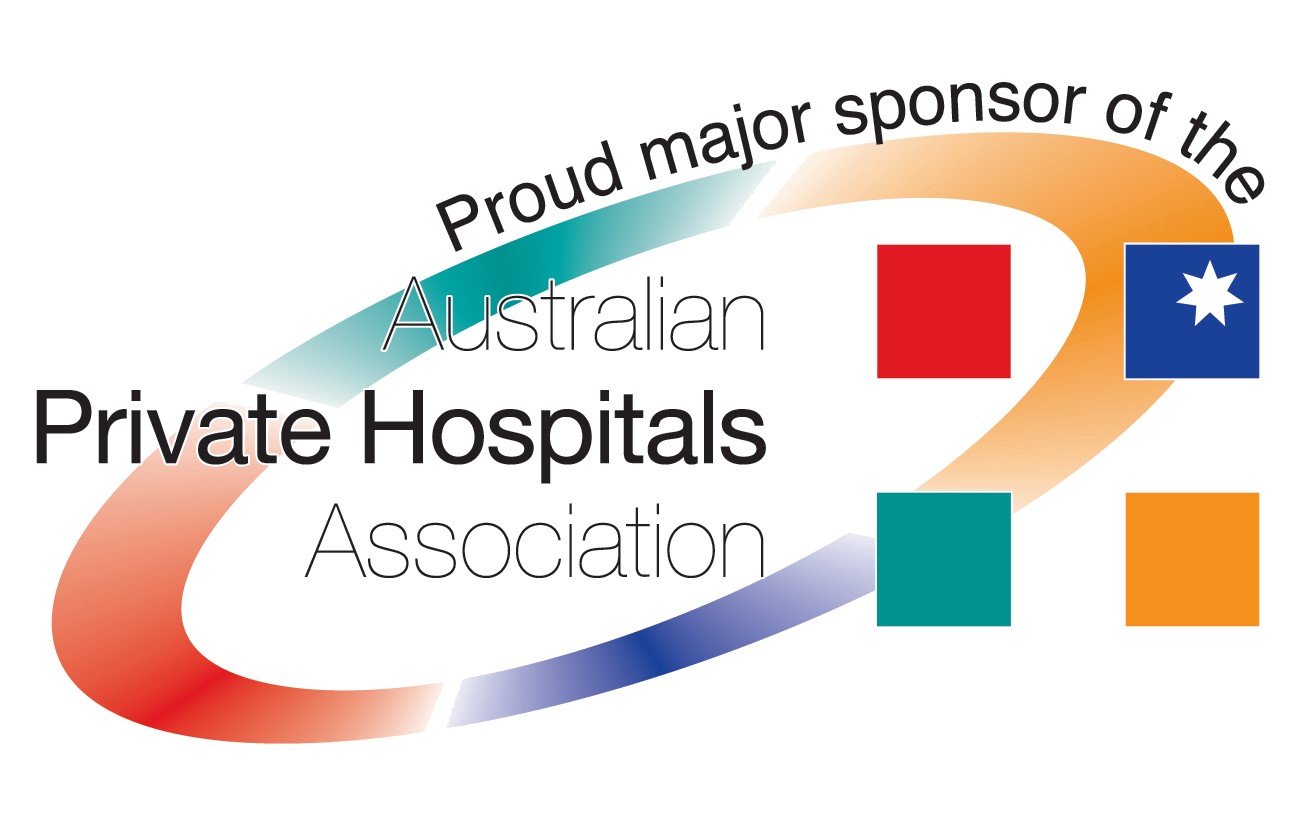
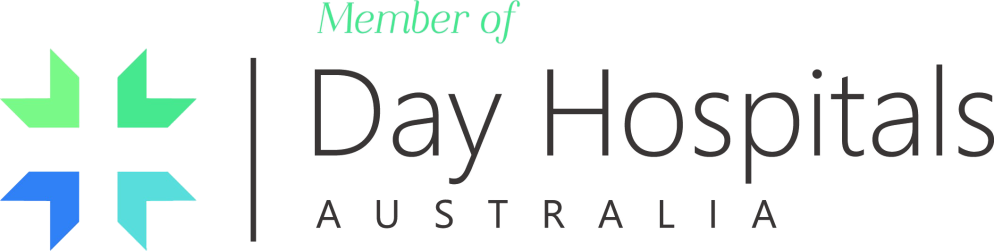
COMPLIANCE
Sterequip is committed to providing an AS 5369 compliant reprocessing solution for Health Service Organisations now and for the future changes to the Standard.
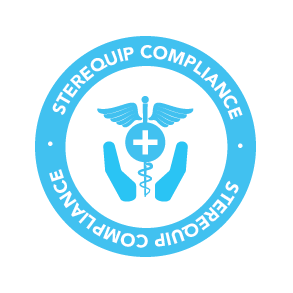