THE STERILISATION STANDARD IN AUSTRALIA HAS CHANGED
Discover What Has Changed Has Changed With AS 5369
Standards Australia AS 5369: 2023 for Reprocessing of reusable medical devices and other devices in health and non-health related facilities has five key considerations you need to know.
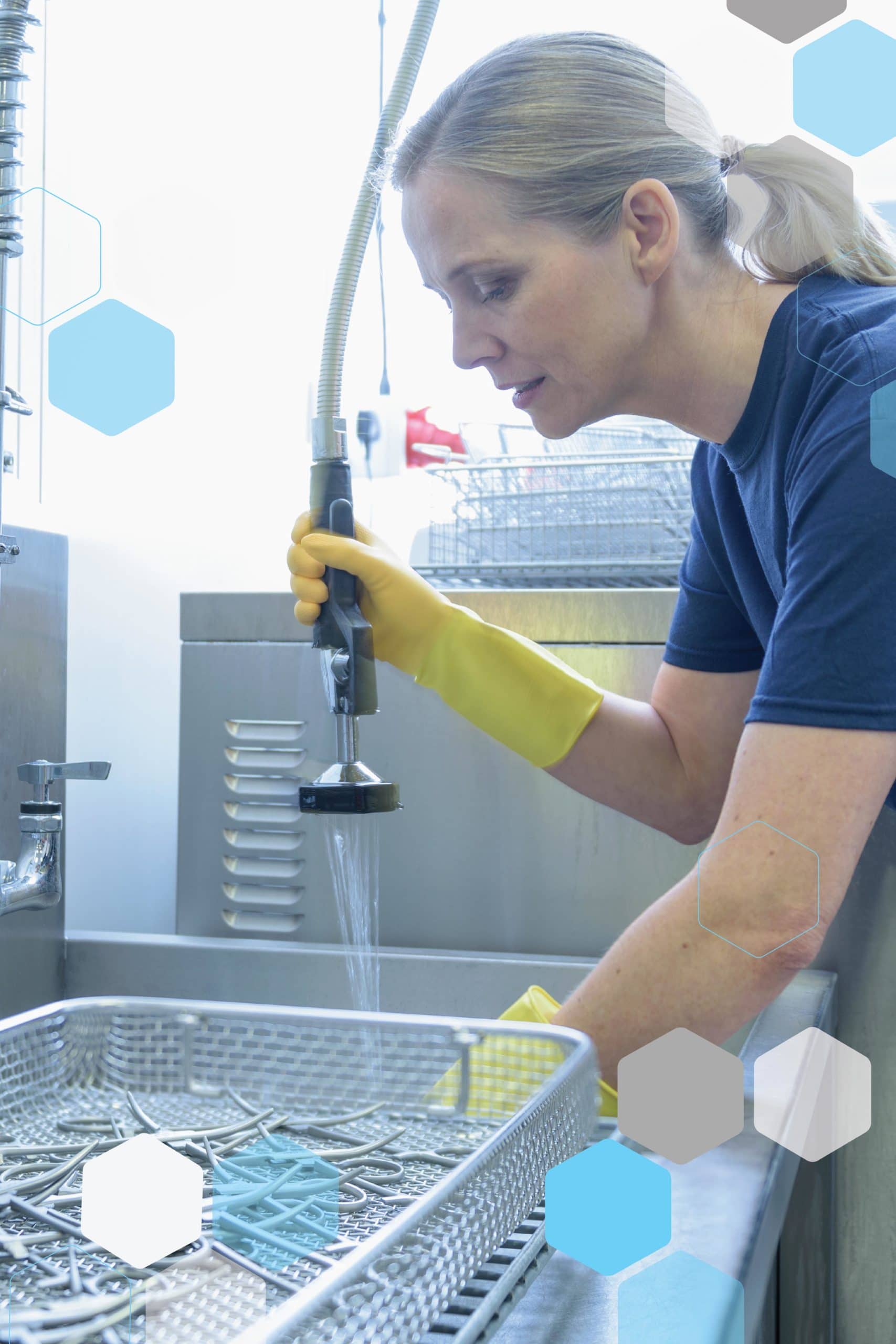
WATER QUALITY
Water quality is a critical consideration in all stages of the reprocessing of reusable medical devices. Softened, filtered, demineralised, reverse osmosis or distilled water needs to be in accordance with the equipment manufacturer’s specifications.
Regular testing and monitoring of water quality is required to assess compliance with the parameters outlined in the Standard. It may be necessary to treat water before using it for reprocessing and sterilisation, such as reverse osmosis.
The key water quality elements that should be considered are:
- Hardness (i.e high mineral content)
- pH value
- Total organic carbon
- Ionic contaminants (e.g. heavy metals, halides, chlorides, phosphates and silicates) and resistivity
- Microbial population
- Bacterial endotoxin
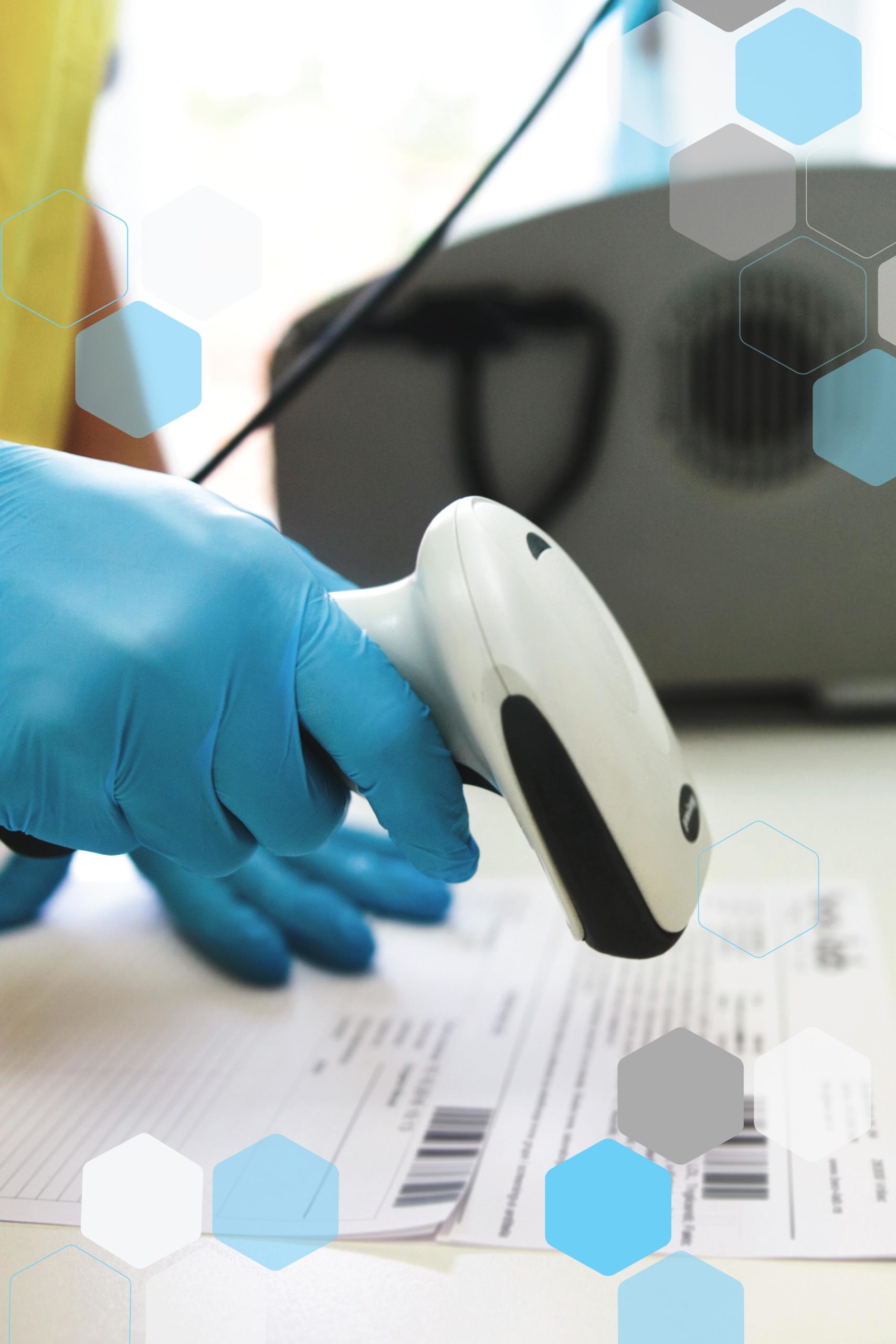
DEVICE IDENTIFICATION & TRACEABILITY
The standard requires that all your instruments are traceable to the patient. Your system needs to identify the cleaning process applied to each Reusable Medical Device, including an ability to track a device to a patient and allow a recall if required.
Instrument tracking has now been introduced in the latest standard and has several benefits, including complete traceability, improved patient safety, enhanced risk management and increased accountability.
In the event that a non-conforming device is used and a recall is necessary, health services must have a traceability system than can identify affected patients.
The Standard notes that Health Service Organisations should be working towards an electronic tracking process and record system.
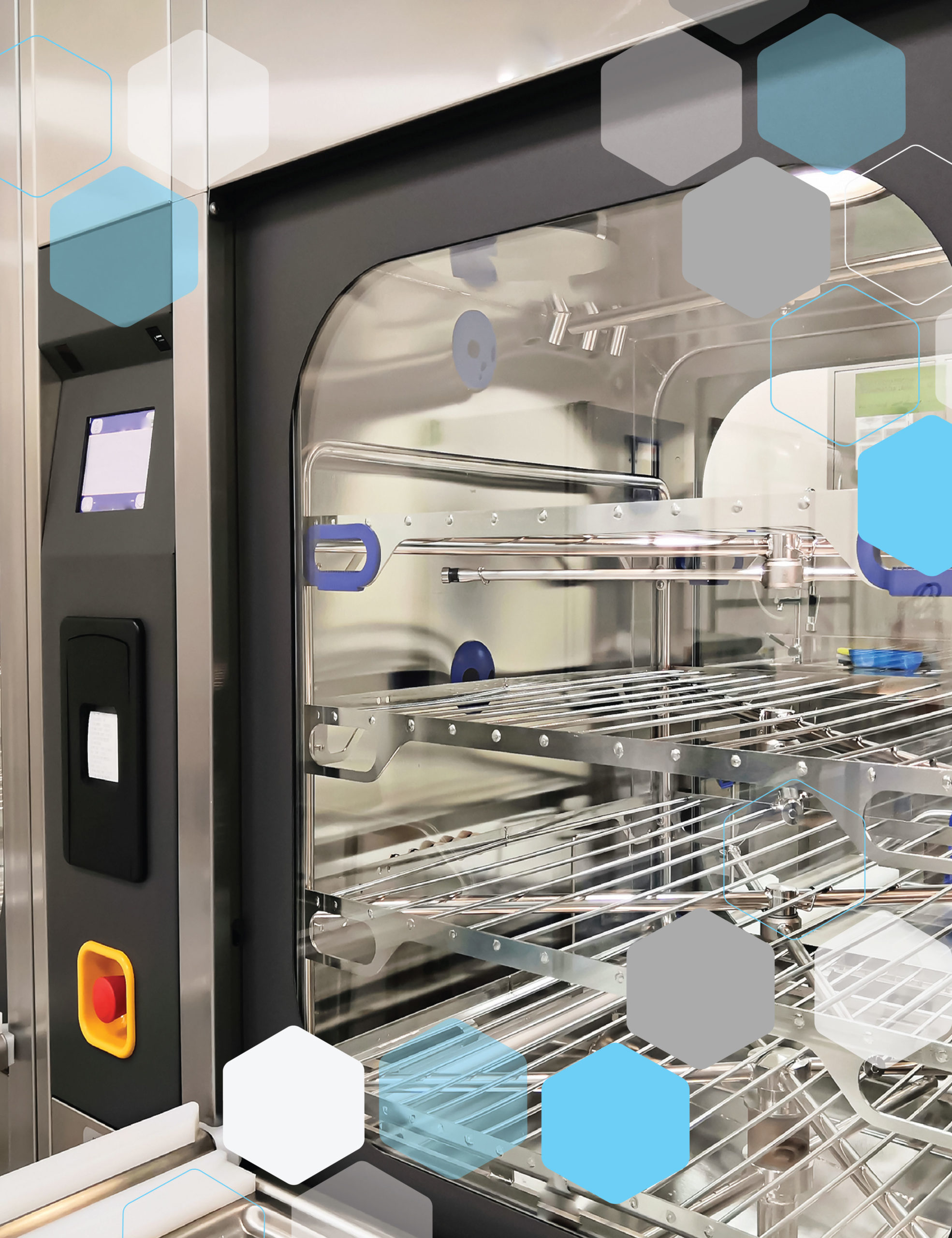
NEW EQUIPMENT
To meet the requirements of the new standard, most Central Sterile Services Departments will need the following new equipment:
A washer disinfector (compliant with ISO 15883)
A steriliser (compliant with EN 285 or EN 13060)
Water supply capable of providing water of the quality laid out in table 7.2 and table 7.3 of AS 5369:2023.
All new equipment must undergo installation qualification (IQ), operational qualification (OQ) and performance qualification (PQ). These tests must be documented and meet the applicable national and international standards.
All Central Sterile Services Department equipment must also be compatible with the detailed specifications provided by Reusable Medical Device manufacturers.
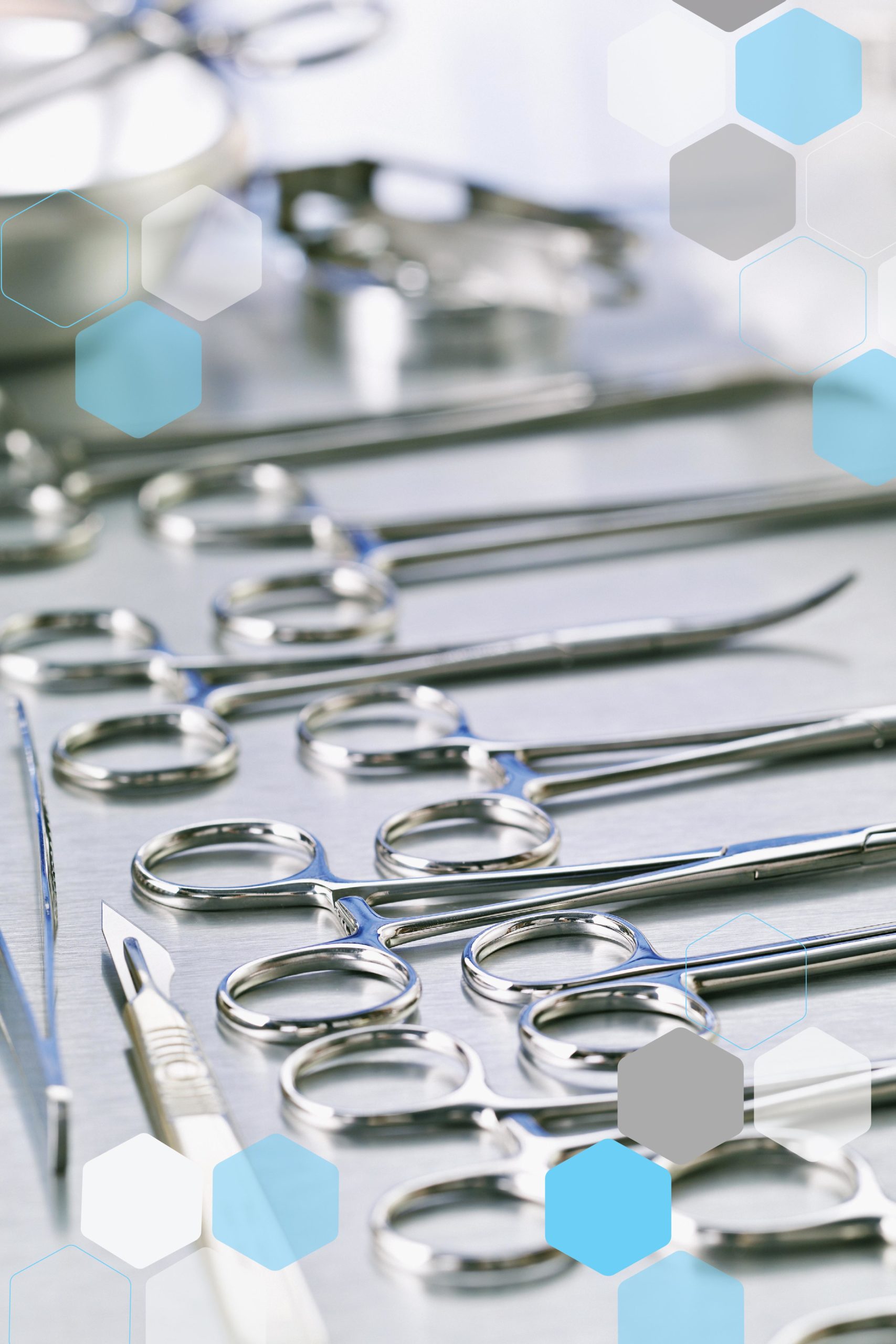
PRODUCT FAMILIES
Reusable medical devices (RMDs) are grouped according to their materials, intended use, design characteristics, physical mass and thermal conductivity.
Grouping devices into product families addresses some of the challenges posed by the increased range of RMDs available and the variety of design, complexity and reprocessing requirements.
You are required to:
Understand and document the product family for each individual device used.
Correctly reprocess each device according to its product family and the manufacturer’s instructions.
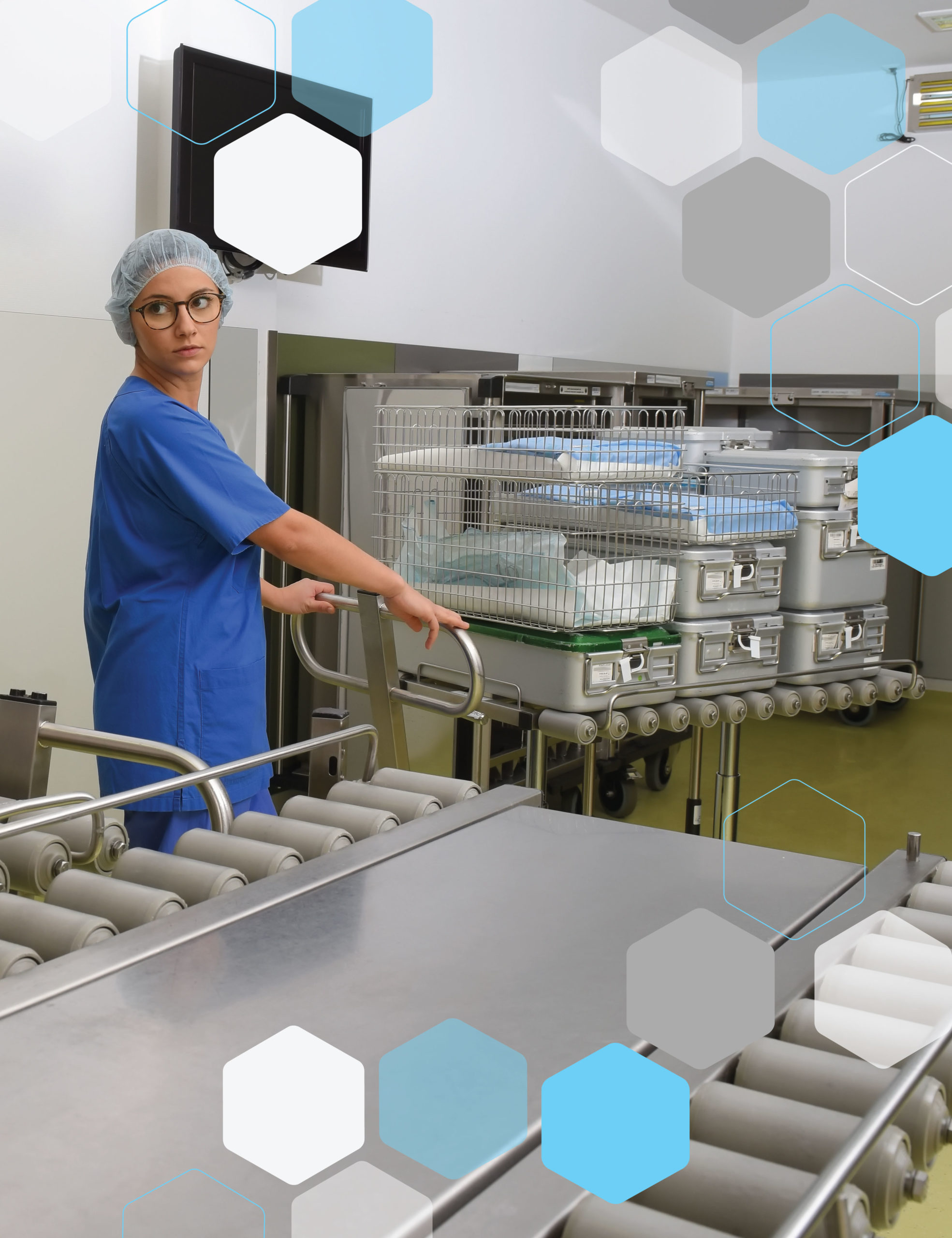
SPACE, LAYOUT & DESIGN
Your Central Sterile Services Department is required to comply with AS 5369 requirements for separate rooms for clean and contaminated reprocessing and ensure unidirectional workflow and airflow to reduce the risk of cross-contamination.
This means physically segregating the reprocessing environment and equipment by redesigning your floor plan and potentially allocating more space to your Central Sterile Services Department.
Reprocessing facilities should be designed, constructed, maintained and controlled to provide effective segregation of clean and dirty activities.
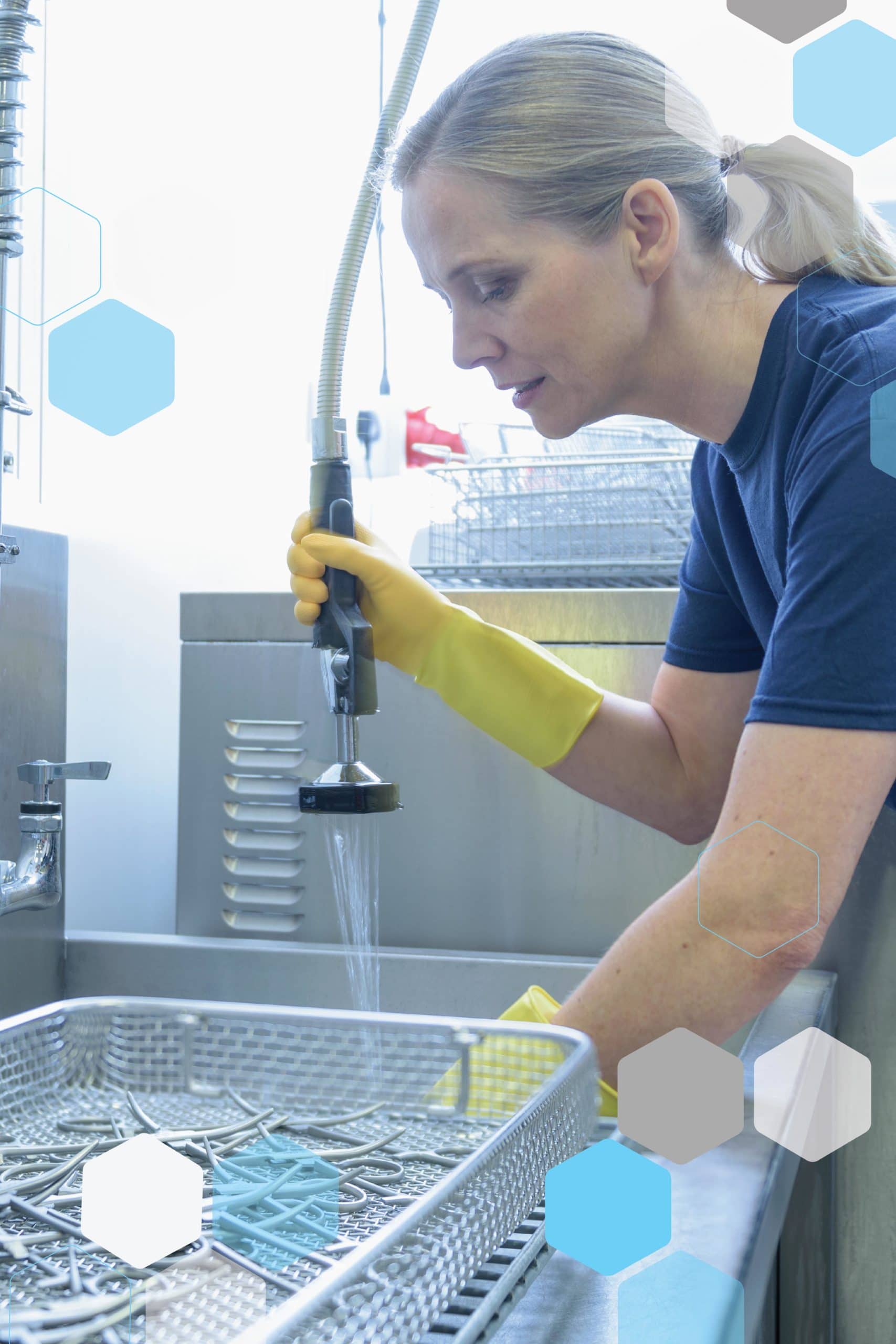
WATER QUALITY
Water quality is a critical consideration in all stages of the reprocessing of reusable medical devices. Softened, filtered, demineralised, reverse osmosis or distilled water needs to be in accordance with the equipment manufacturer’s specifications.
Regular testing and monitoring of water quality is required to assess compliance with the parameters outlined in the Standard. It may be necessary to treat water before using it for reprocessing and sterilisation, such as reverse osmosis.
The key water quality elements that should be considered are:
- Hardness (i.e high mineral content)
- pH value
- Total organic carbon
- Ionic contaminants (e.g. heavy metals, halides, chlorides, phosphates and silicates) and resistivity
- Microbial population
- Bacterial endotoxin
DEVICE IDENTIFICATION & TRACEABILITY
The standard requires that all your instruments are traceable to the patient. Your system needs to identify the cleaning process applied to each Reusable Medical Device, including an ability to track a device to a patient and allow a recall if required.
Instrument tracking has now been introduced in the latest standard and has several benefits, including complete traceability, improved patient safety, enhanced risk management and increased accountability.
In the event that a non-conforming device is used and a recall is necessary, health services must have a traceability system than can identify affected patients.
The Standard notes that Health Service Organisations should be working towards an electronic tracking process and record system.
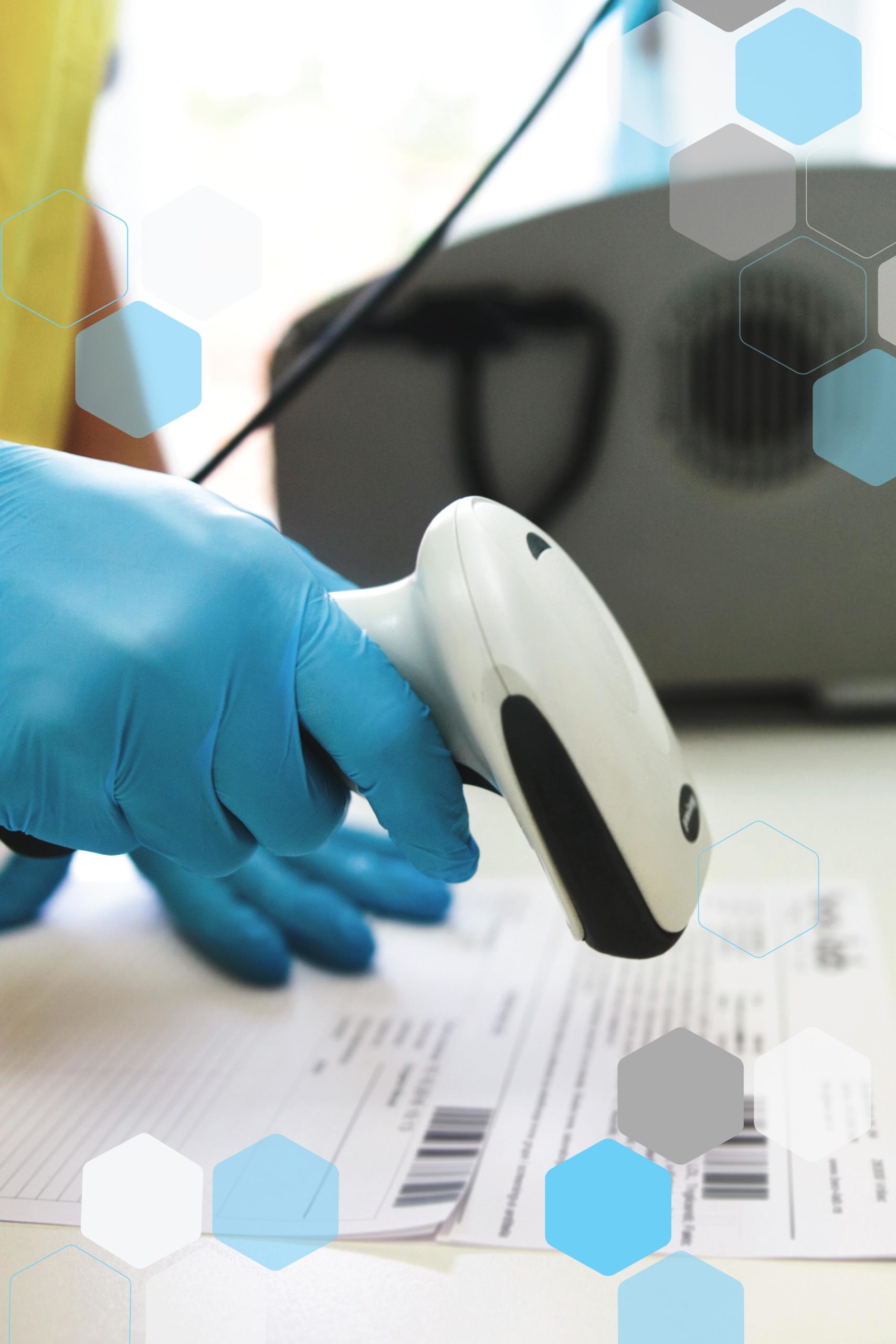
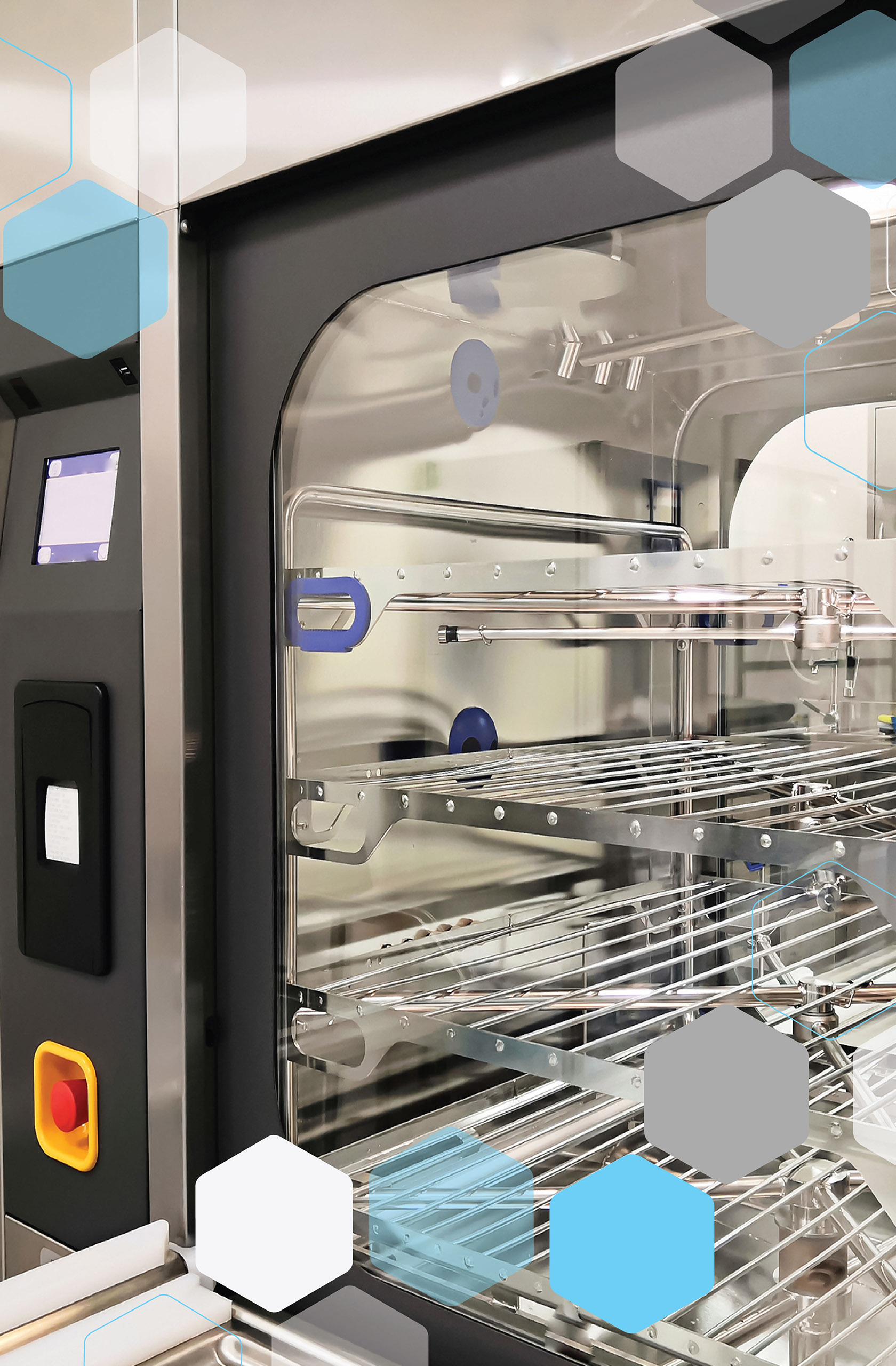
NEW EQUIPMENT
To meet the requirements of the new standard, most Central Sterile Services Departments will need the following new equipment:
- A washer disinfector (compliant with ISO 15883)
- A steriliser (compliant with EN 285 or EN 13060)
- Water supply capable of providing water of the quality laid out in table 7.2 and table 7.3 of AS 5369:2023.
All new equipment must undergo installation qualification (IQ), operational qualification (OQ) and performance qualification (PQ). These tests must be documented and meet the applicable national and international standards.
All Central Sterile Services Department equipment must also be compatible with the detailed specifications provided by Reusable Medical Device manufacturers.
PRODUCT FAMILIES
Reusable medical devices (RMDs) are grouped according to their materials, intended use, design characteristics, physical mass and thermal conductivity.
Grouping devices into product families addresses some of the challenges posed by the increased range of RMDs available and the variety of design, complexity and reprocessing requirements.
You are required to:
- Understand and document the product family for each individual device used.
- Correctly reprocess each device according to its product family and the manufacturer’s instructions.

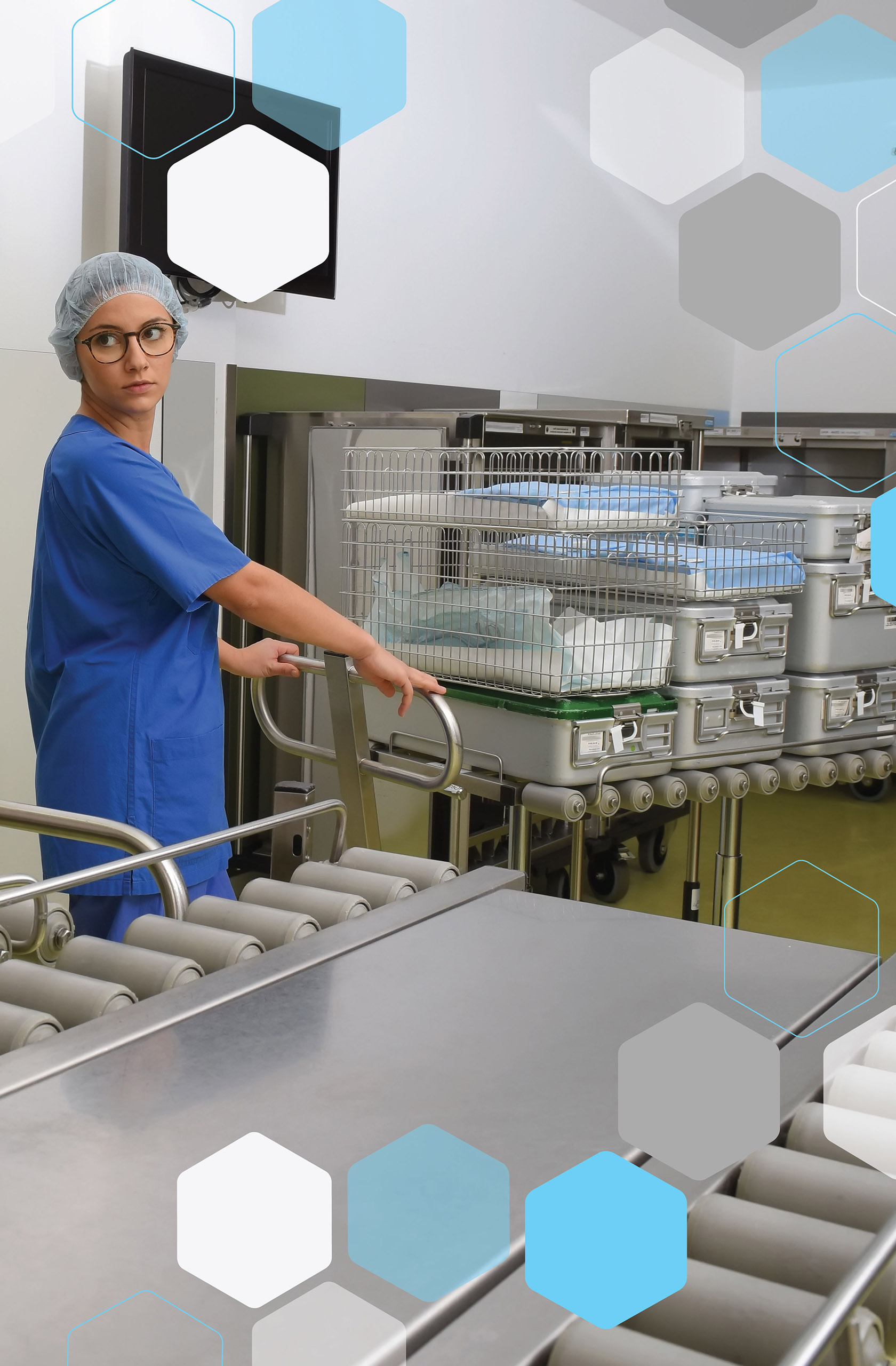
SPACE, LAYOUT & DESIGN
Your Central Sterile Services Department is required to comply with AS 5369 requirements for separation and ensure unidirectional workflow and airflow to reduce the risk of cross-contamination.
Physically segregating the reprocessing environment and equipment by redesigning your floor plan can mean potentially allocating more space to your Central Sterile Services Department.
Reprocessing facilities should be designed, constructed, maintained and controlled to provide effective segregation of clean and dirty activities.